Для российских партнеров:
Для казахских партнеров:
Для узбекских партнеров
Корзина Корзина
0
Воспользуйтесь каталогом, положите товар в корзину и оформите заказ.
- Стандарты
- Черные металлы и сплавы
- Цветные металлы и сплавы
- Специальные стали и сплавы
- Сварочные материалы
- Трубный прокат
- Детали трубопровода
- Арматура трубопроводная
- Черный металлопрокат
- Цветной металлопрокат
- Крепеж, метизы
- Подшипники
- Пружины
- Сетка
- Статьи и сводные таблицы
- Футеровка (бронировка)
- Оборудование и инструменты
- Днища
Отправьте заявку
в WhatsApp
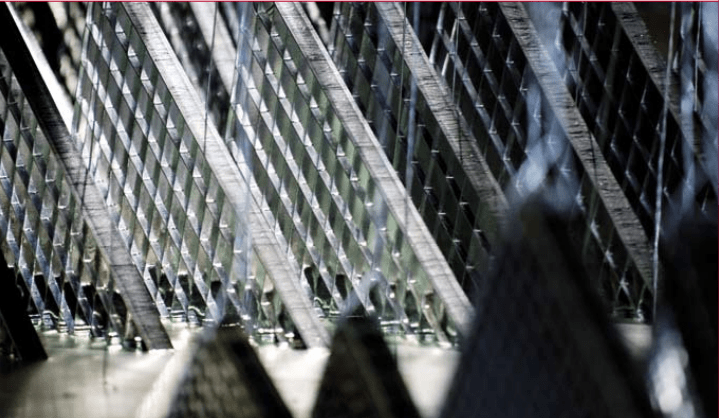
Технология горячего оцинкования с момента появления и по сегодняшний день является наиболее простым, эффективным и экономически выгодным методом антикоррозийной защиты металлических изделий и конструкций. Средний срок их эксплуатации после оцинкования составляет от 50 до 70 лет.
А исследования American Galvanizer Association свидетельствуют о большей продолжительности службы изделий и конструкций с оцинкованным покрытием, что зависит от условий эксплуатации.Так, в производственных условиях – до 65 лет, в условиях жары и повышенной влажности – до 70 лет, в городских условиях – до 85, а на открытом воздухе за городом – до 120 лет.
В современных условиях горячее оцинкование выполняют на инновационном оборудовании линии оцинкования компании "Western Technologies" (известного во всех странах мира производителя оборудования этой категории).
Для изделий и конструкций из металла оцинкование горячим способом, безусловно, считается наиболее популярным и эффективным типом антикоррозионной защиты.
А в 1836 г. химик С. Сорель (Франция) оформил патент на этот способ оцинкования.
Сорель использовал понятие «цинкование», так как обнаружил, что металл защищает воздействие гальванического тока, даже при повреждении покрытия. Это происходит, потому, что цинк и железо вступают в контакт при электрическом влиянии.
В основе технологии горячего оцинкования лежит принцип химического соединения. Под воздействием среды возникает цепь химических реакций:
После оцинкования покрытие должно выглядеть сплошным, не иметь трещин, вздутий, вмятин. Допустим цвет - от блестящего светло-серебристого до матового тёмно-серого. При не покрытии некоторых участков цинком, их можно восстановить, но только в тех случаях, если их ширина не превышает 2,0 см, и общая площадь непокрытого изделия составляет менее 2 %. При этом,прочность и стойкость антикоррозийного покрытия металла не зависят от его внешнего вида и цвета.
в WhatsApp
- Главная
- Энциклопедия
- Решётчатый настил
- Горячее оцинкование
Горячее оцинкование
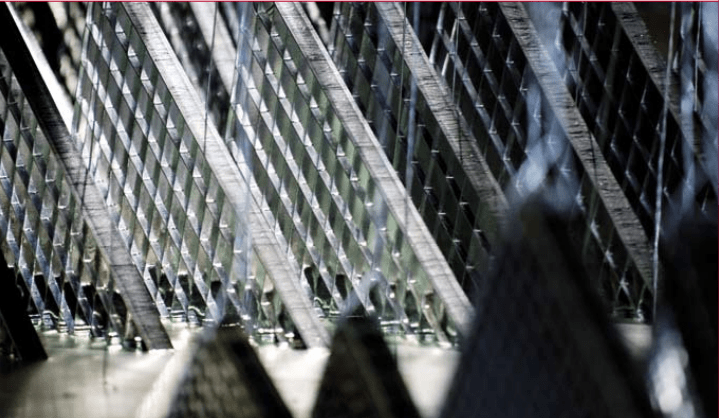
Технология горячего оцинкования с момента появления и по сегодняшний день является наиболее простым, эффективным и экономически выгодным методом антикоррозийной защиты металлических изделий и конструкций. Средний срок их эксплуатации после оцинкования составляет от 50 до 70 лет.
А исследования American Galvanizer Association свидетельствуют о большей продолжительности службы изделий и конструкций с оцинкованным покрытием, что зависит от условий эксплуатации.Так, в производственных условиях – до 65 лет, в условиях жары и повышенной влажности – до 70 лет, в городских условиях – до 85, а на открытом воздухе за городом – до 120 лет.
В современных условиях горячее оцинкование выполняют на инновационном оборудовании линии оцинкования компании "Western Technologies" (известного во всех странах мира производителя оборудования этой категории).
Для изделий и конструкций из металла оцинкование горячим способом, безусловно, считается наиболее популярным и эффективным типом антикоррозионной защиты.
Из истории открытия метода
В 1742 г. впервые появилось описание способа оцинкования железа путём погружения его в ванну(керамическую ёмкость) с расплавленным цинком. Это был доклад Поля Жака Малуэна нафранцузской Королевской академии.А в 1836 г. химик С. Сорель (Франция) оформил патент на этот способ оцинкования.
Сорель использовал понятие «цинкование», так как обнаружил, что металл защищает воздействие гальванического тока, даже при повреждении покрытия. Это происходит, потому, что цинк и железо вступают в контакт при электрическом влиянии.
Технология оцинкования
Способ нанесения покрытия состоит из нескольких этапов. После предварительных процедур -обезжиривания, промывания, травления и вторичного промывания, изделия, помещённые в барабан, опускают в ёмкость с расплавленным при температуре 460 °C, цинком. Барабан,вращаясь, создаёт поток жидкого цинка, который, обтекая все металлические детали, заполняетвсе микротрещины изделия. По окончании процесса барабан поднимают из ёмкости ираскрывают, чтобы при помощи центрифуги удалить остатки лишнего цинка. Однако полностью их снять не удаётся, например, они остаются на внутренней резьбе, поэтому её необходимо протачивать. Толщина покрытия цинком при оцинковании колеблется в диапазоне от 30 мкм до100 мкм, наиболее часто применяется оцинкование с толщиной слоя 45-65 мкм.В основе технологии горячего оцинкования лежит принцип химического соединения. Под воздействием среды возникает цепь химических реакций:
- цинк + кислород = оксид цинка;
- образованный оксид цинка + двуокись углерода = карбонат цинка.
Требования к изделиям и конструкциям, подвергающимся оцинкованию
- Габариты изделий не должны превышать габариты ванны.
- Материал изготовления конструкции, изделия должен поддаваться оцинкованию
- Оцинкование изделий, имеющих сварные соединения типа «внахлест», не допускается. В таких случаях швы необходимо закольцовывать.
- В конструкциях и изделиях должны отсутствовать закрытые полости, карманы, в противном случае к ним будет закрыт доступ потока расплавленного цинка.
После оцинкования покрытие должно выглядеть сплошным, не иметь трещин, вздутий, вмятин. Допустим цвет - от блестящего светло-серебристого до матового тёмно-серого. При не покрытии некоторых участков цинком, их можно восстановить, но только в тех случаях, если их ширина не превышает 2,0 см, и общая площадь непокрытого изделия составляет менее 2 %. При этом,прочность и стойкость антикоррозийного покрытия металла не зависят от его внешнего вида и цвета.
Основные этапы процесса согласно норме EN ISO 1461
- Обезжиривание – для чего изделие опускают в щелочной раствор.
- Травление - в растворе соляной кислоты.
- Флюсовка - в растворе хлорида аммония и хлорида цинка.
- Сушка – при температуре 100 °С.
- Оцинкование – в расплавленном цинке при температуре 450-460 °С.
- Менее 1,5 мкм – 45 мм;
- От 1,5 до 3,0 мкм – 55 мм;
- От 3,0 до 6,0 мкм – 70 мм;
- Свыше 6,0 мкм – 85 мм.
Обработка после процесса оцинкования
После оцинкования с покрытия необходимо зачистить все дефекты, которые могут возникнуть во время процесса – пузыри, локальные шероховатости, вздутия и вмятины, заострённые места.Эффективность горячего оцинкования
Покрытие горячим цинком эффективно без дополнительной защиты при эксплуатации конструкций и изделий в различных средах, в разных условиях и режимах.- В любых вентилируемых помещениях.
- На открытых участках.
- При контактах с водой повышенной жёсткости (температура до 60 °С).
- При эксплуатации под землёй.
- При контактах с любыми металлами (за исключением погружения в расплавленные металлы).
- При длительном воздействии температур до 200 °C или однократном – до 275 °С.
Факторы, влияющие на качество оцинковки
На качество цинкового покрытия оказывают влияние разные факторы:- Температура плавления цинка (не выдерживание температуры в 450-460 °С, чревато нарушением процесса).
- Соответствие химического состава стали - углерод и кремний менее 0,25 %. В противном случае существенно хуже внешний вид покрытия.
- Тщательность очистки и подготовки поверхностей – при нарушении требований по очистке расплавленный цинк неравномерно распределяется по поверхности, и плохо вступает в реакции с металлом изделия, что провоцирует появление большого количества дефектов. Некачественная сушка поверхности приводит к непокрытым участкам, слабому сцеплению и неравномерности слоя.
- Скорость, с которой изделие опускают в расплавленный цинк – постепенное погружение, это гарантия хорошей обтекаемости горячим цинком всего изделия, при быстром опускании возможны дефекты поверхности (так как флюс не имеет возможности полностью расплавиться).
- Скорость, с которой изделие вынимают из ванны – фактор, от которого зависит, какова будет толщина слоя покрытия. Чем медленнее происходит подъём, тем больше будет толщина слоя, что определяется скоростью, с которой происходит кристаллизация жидкого цинка. Для всех изделий с нестандартными формами скорость и наклон при подъеме устанавливают в каждом конкретном случае.
- Время нахождения деталей в жидком цинке – зависит от того, как долго температуры жидкого горячего цинка и собственно изделия сохраняются на одном уровне.
Достоинства технологии оцинкования
Одно из важнейших достоинств метода горячего оцинкования заключается в том, что этот процесс обеспечивает защиту двойного типа – механическую и электрохимическую.- Покрытие цинком препятствует непосредственному контакту поверхностям изделий с внешней средой. Это обусловлено тем, что цинк, за счёт своей активности, под влиянием агрессивных сред образует прочную и плотную плёнку, снижающую скорость образования коррозии.
- Цинк в гальванической паре выступает в качестве анода, а железо - катода, поэтому цинковый слой принимает на себя разрушительное воздействие электрохимической коррозии. При этом, элементы электрохимической коррозии могут скапливаться на участках сколов, повреждений, и образуют механическое препятствие, «исправляя» разрушения покрытия.
Другие материалы

Комплексные поставки

Сервисные услуги

Контроль качества

Персональный менеджер проекта

«Точно в срок» (Just In Time)

Полный пакет документов